FOODTOWNアドバイザーが
食品工場見える化(システム)を徹底解説!
FOODTOWNアドバイザーが
食品工場見える化(システム)を徹底解説!
食品工場見える化(システム)とは?
食品工場や製造現場では、情報の共有が非常に重要となります。広い製造現場の中で対面対話のみでの情報のやり取りでは非効率となってしまいます。様々な項目を見える化(可視化)することによって整理された情報をタイムリーに取得することができるシステムが「見える化」というものです。
食品業界に限らず、工場や製造現場ではあらかじめ設定されたQCDに沿って生産活動を行います。QはQuality(品質)、CはCost(コスト)、DはDelivery(納期)となり、その全てを達成する必要があります。
食品工場に「見える化」システムを導入して、生産進捗状況、ロス率歩留まり、出荷実績、在庫状況などの様々な情報が数値化、可視化された環境を構築することで、情報取得の手間を省き、見えない不安が解消します。
適正在庫、歩留まり率の向上、生産性の向上など課題も見えやすくなるため改善活動にも効果が期待できます。
見える化システムの種類、使用用途、確認ポイントについて解説します。
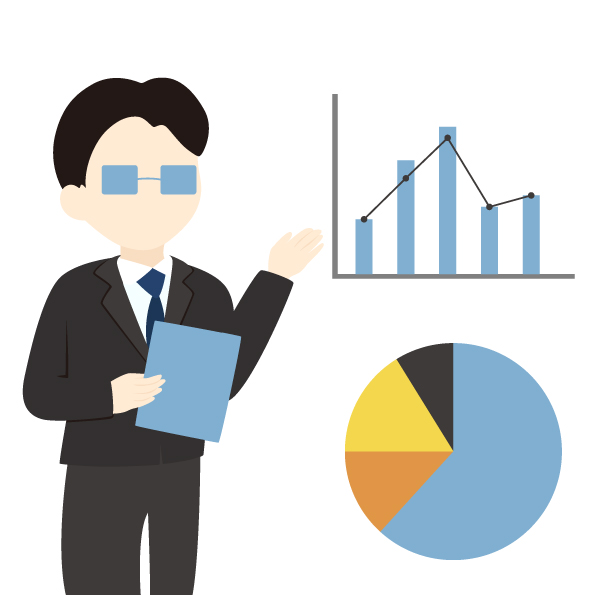
-
食品工場の見える化の種類、原理、使用用途について
-
食品工場見える化導入価格について
-
食品工場見える化選定ポイント、導入時の確認ポイントについて
-
食品工場見える化導入後のトラブル事例と事前対策ポイントについて
製品詳細確認・カタログ無料ダウンロード可能
「いろんな製品があって選ぶ基準が分からない…」そんなアナタに
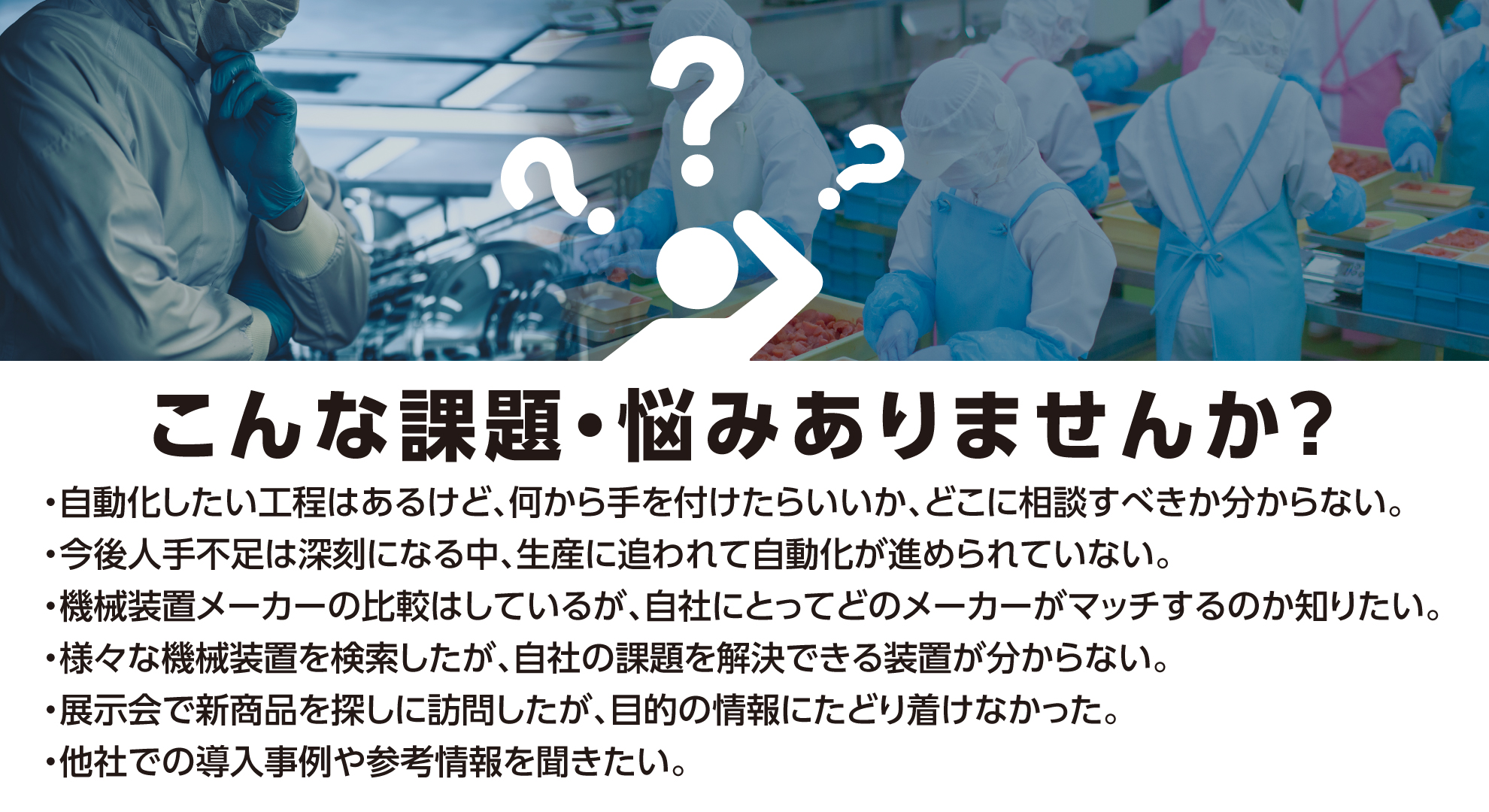

ヒアリングシート
3つのメリットと特徴
-
MERIT 1
- 自動化すべき工程が
明確になる! - 相談は3分で登録完了。自動化したい工程と製造条件を選択するだけ!
- 自動化すべき工程が
-
MERIT 2
- 相談するだけで最適な
メーカー紹介に繋がる! - 1,000社、10,000を超える商品から最適な情報を紹介!
- 相談するだけで最適な
-
MERIT 3
- 補助金や助成金の
情報紹介も可能! - 自動化するために活用できる全国の補助金情報も紹介!
- 補助金や助成金の
IoT・生産管理・効率化システムの商品種別から他の解説記事を探す